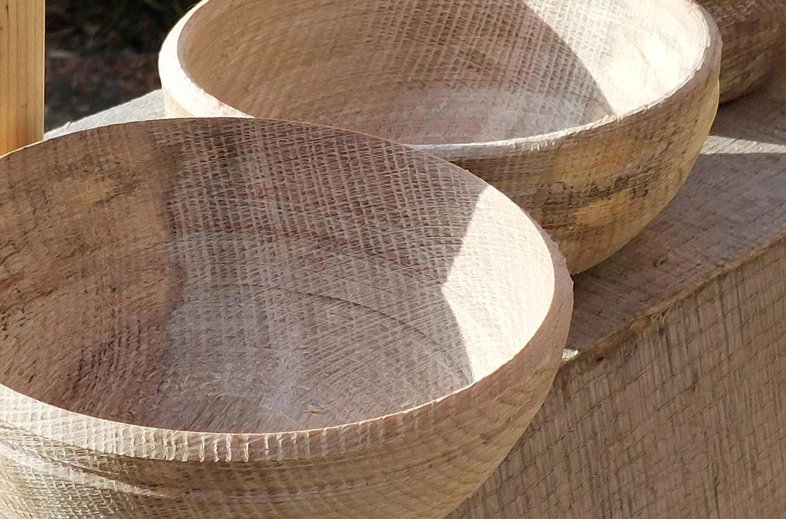
Choosing the right type of wood is crucial for any woodturning project. Still, it becomes particularly significant when turning bowls, where the wood’s characteristics can profoundly impact the process and the final product. As a pole-lathe turner, my experiences have taught me that not just any wood will do, especially when it comes to creating pieces that are not only beautiful but also functional and durable.
In this article, I’ll delve into what makes greenwood ideal for bowl turning and how its natural properties can influence the turning experience. From understanding the basics of greenwood to selecting the best species based on moisture content, durability, and aesthetic appeal, I aim to provide a comprehensive guide that s
helps novices and experienced turners make informed decisions. Join me as we explore the fascinating interplay between wood and lathe, discovering how the right choice at the outset can enhance the beauty and longevity of your turned bowls.
What is Greenwood?
Any tree that has recently been felled is termed greenwood. It means the wood hasn’t dried out. This does create some challenges for a pole-lathe turner:
Checks and cracks
Wooden logs don’t dry evenly. They lose moisture from the cut ends far quicker than at the centre of the log. This causes a lot of pressure within the log. As the pressure increases as the green wood dries the wood cracks, or as it’s known in the industry, it checks.
How green should the wood be?
Some trees hold more moisture than others. For example, I’ve turned freshly cut sycamore and been covered in a thin layer of sap as it is thrown out of the wood as it turns. The main drawback (other than being covered in sap) is that the finish on the bowl isn’t as good as when the wood is a little drier.
However, it’s also important that the wood isn’t too dry. You indeed get a better finish, but it also makes working the wood much harder and you spend a lot more time sharpening your tools.
Understanding Wood Types: Ring Porous vs. Diffuse Porous Woods
When embarking on a woodturning project, particularly when turning bowls on a pole-lathe, one of the key considerations is the type of wood to use. Understanding the distinction between ring porous and diffuse porous woods is essential as it impacts not only the workability of the wood but also the finish and durability of the final product.
Ring Porous Woods
Characteristics: Ring porous woods, such as oak and ash, are characterized by having large pores in the earlywood and smaller, denser pores in the latewood. This distinct pattern results in visible annual growth rings, which not only add a unique aesthetic to any piece but also have practical implications in woodturning.
Workability: The large earlywood pores absorb finishes differently than the denser latewood, which can lead to interesting effects when applying stains or finishes. However, this can also pose a challenge as the uneven absorption might require additional attention during finishing to achieve a uniform appearance.
Best Uses: Due to their structural strength, ring porous woods are excellent for projects that require durability. Their pronounced grain patterns make them popular choices for decorative bowls or items that are as much a focal point in home decor as they are functional pieces.
Diffuse Porous Woods
Characteristics: In contrast, diffuse porous woods like maple, cherry, and beech feature a more uniform distribution of smaller pores throughout the wood, without a clear distinction between the earlywood and latewood. This gives them a more consistent grain pattern and texture, which is often sought after for its aesthetic qualities.
Workability: These woods are generally easier to work with on a lathe because of their uniform density, which allows for smoother cutting and less risk of tear-out. Diffuse porous woods typically absorb finishes more evenly, which can simplify the finishing process and help achieve a fine, smooth surface ideal for high-quality bowls.
Best Uses: The consistency and subtle grain patterns of diffuse porous woods make them suitable for finely detailed work. They are often chosen for their ability to showcase precise craftsmanship and intricate designs, making them favorites for artistic bowls, ornamental pieces, and fine kitchenware.
Choosing the Right Wood
Whether to choose a ring porous or diffuse porous wood will largely depend on the specific requirements of your project and the desired aesthetic. Consider the end use of the bowl—will it be purely decorative, or will it need to withstand frequent handling? The answer will guide your wood choice, balancing between beauty and functionality. As always, personal preference plays a significant role; each woodturner will have their favorites based on past experiences and the unique characteristics they prefer to work with.
Understanding these wood types not only enhances your ability to select the right material but also enriches your appreciation of how these natural materials contribute to the art and craft of woodturning.
Sourcing Greenwood
Finding a reliable source of greenwood can be challenging. One potential option is to contact local tree surgeons. Tree surgeons are professionals who remove and trim trees, and they may have access to various wood types. They may also be able to give you information about the wood, including what type of tree it came from, the age and condition of the wood, and whether it was sustainably sourced. Additionally, you can check out local sawmills and wood suppliers for green wood. They may have a good stock of green wood, which can be used for various purposes. This can also be a good way to buy wood that is sourced from sustainably managed forests.
Storing Greenwood
Once you have found any quantity of greenwood it can be stored for a few months if kept properly. Some turners have the luxury of allowing the wood to remain where it was felled in the woods or at least close by. For me, I store greenwood behind my garage in the garden. I have chosen a northerly-facing section of the garden that is also in the shade most of the day.
You can slow down the drying process by storing the wood if you follow these steps:
- Don’t cut the logs smaller than you have to.
- Seal the cut ends of the logs with PVA glue or similar.
- Cover the wood with a tarp to protect the wood from wind and sunlight
A note of caution when storing any wood.
There is always a risk that greenwood contains woodworm. Nobody wants to bring woodworm into their home, so I strongly recommend storing untreated wood away from buildings.
So, back to the question:
What is the best wood for turning bowls?
The requirement for greenwood rules out any kind of exotic woods. I also prefer to turn hardwoods over softwood because the bowls are more durable once completed and wood like pine can be very sticky while green.
The best-turning wood is a matter of personal preference, as various factors come into play, including workability, finish, and stability. However, many woodturners often gravitate towards hardwoods such as maple, cherry, walnut, and oak for their exceptional qualities. Maple is highly regarded for its uniform grain and smooth finish, making it ideal for intricate turnings. Cherry offers an appealing reddish hue and a fine, straight grain that finishes exceptionally well. Walnut, with its rich, dark tones, provides an air of sophistication and durability, while oak offers impressive strength and a distinctive grain pattern that lends itself well to various turning projects. Ultimately, the best turning wood depends on the desired aesthetic, functionality, and individual woodworking preferences.
As you will see on my online shop, I turn a lot of English oak bowls, it has a unique grain pattern and it can come in a range of colours from a light beige through red, yellow and to a deep chocolate brown.
Oak for bowl turning
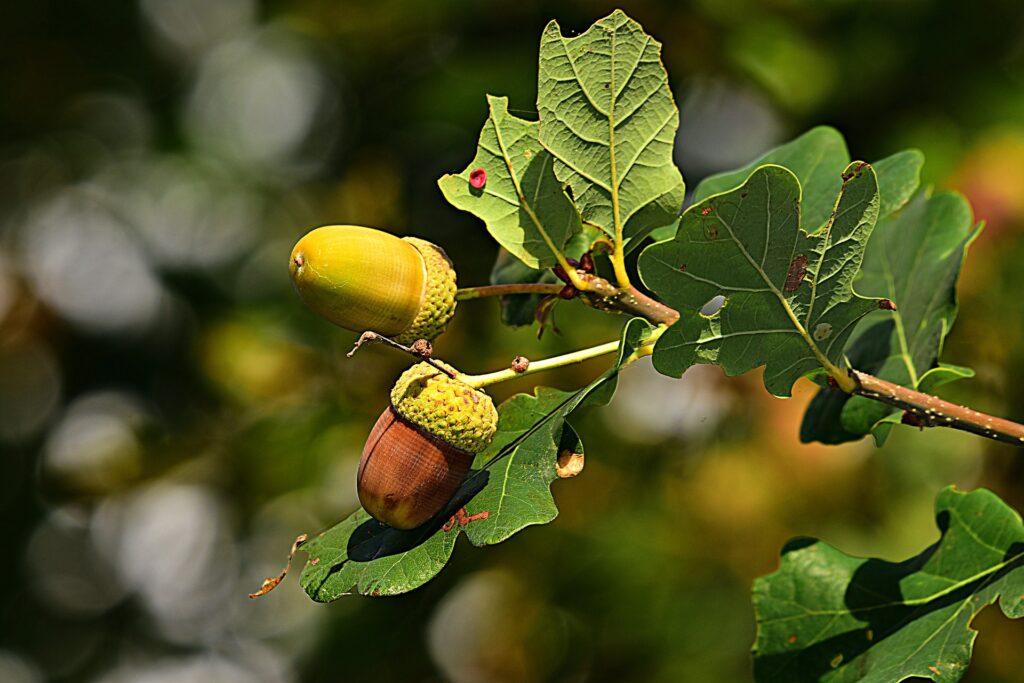
Oak is a robust ring porous wood that turns relatively well whilst it’s still green. It is possible to get a good finish on oak and the grain is interesting once the bowl is finished and oiled.
Challenges of turning oak
During the turning process, oak can become brittle. If you are attempting to turn a bowl with thin walls (3 – 4mm) it is quite easy to break the rim. Oak is also quite fibrous, which can make it difficult to get a good finish on parts of the bowl that have strong edges. For example, the rim or the edge around the foot of the bowl.
Maple
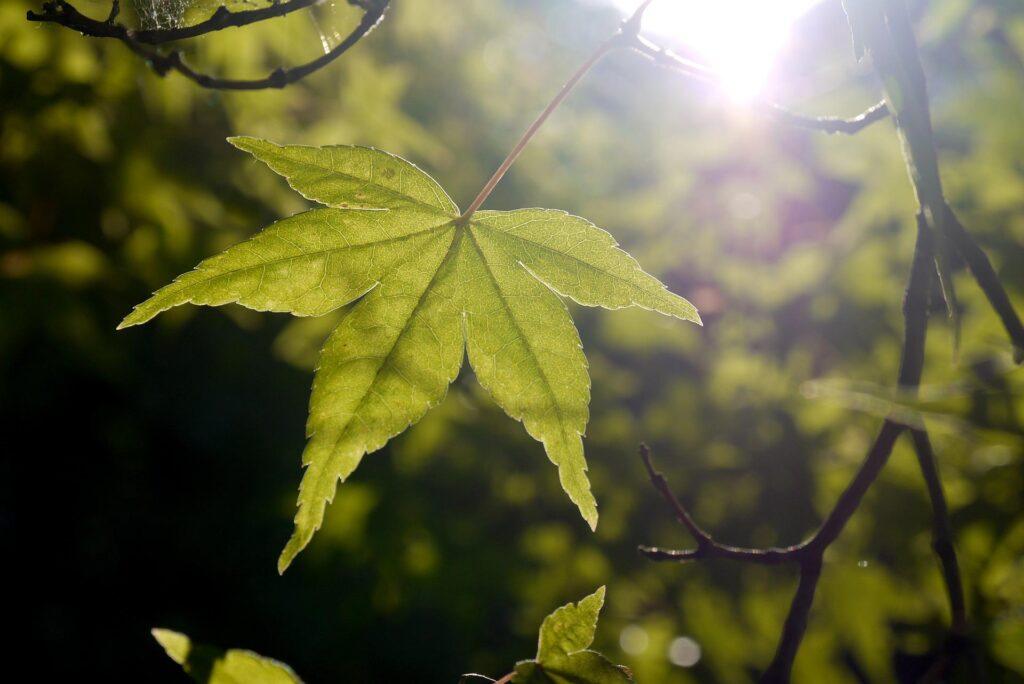
Maple is a diffuse porous hardwood with a fairly straight fine grain, this means you can get a good finish easily. If you experience any tear-out where the finish is looking rough then you need to sharpen your tools.
There are several types of maple including curl, birds-eye, tiger and spalted maple. This range delivers a beautiful range of grain patterns.
Challenges of turning maple
You should allow maple to mature a little on the wood pile. When it’s freshly cut it doesn’t take a finish particularly well.
Cherry for bowl turning
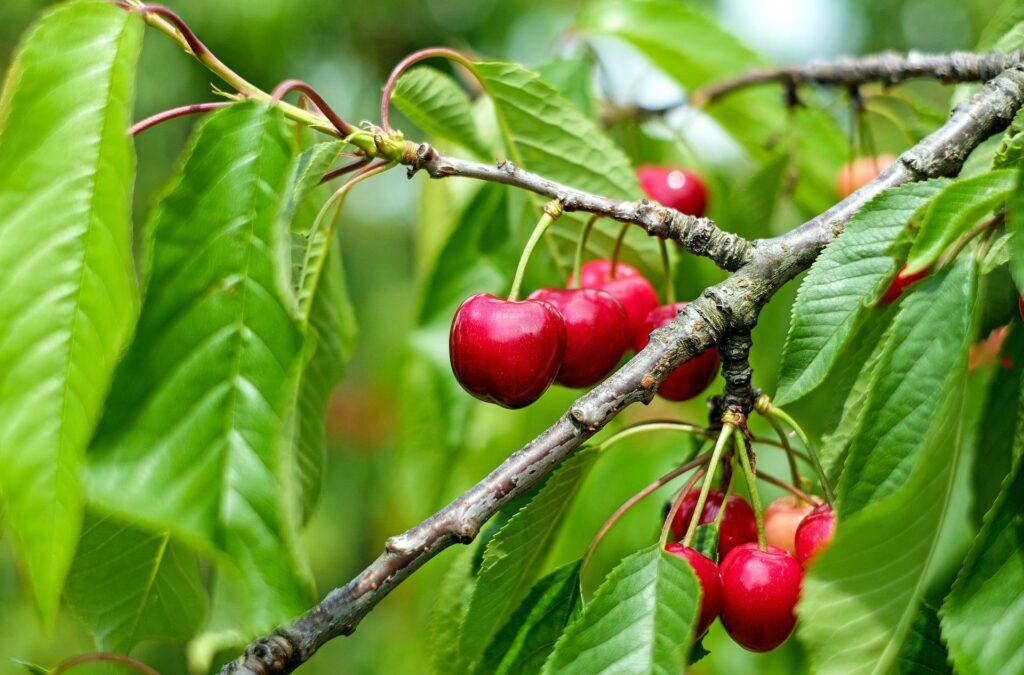
Cherry is one of the more attractive diffuse porous woods to turn. There is often a high contrast between sapwood and heartwood. It is possible to get a very smooth finish on cherry.
Challenges of turning cherry
When turning cherry bowls, it is vitally important to keep the walls and the bowl’s base thin to help prevent cracks as it dries. Drying the bowl slowly will also help reduce the chance of cracks.
Beech for bowl turning
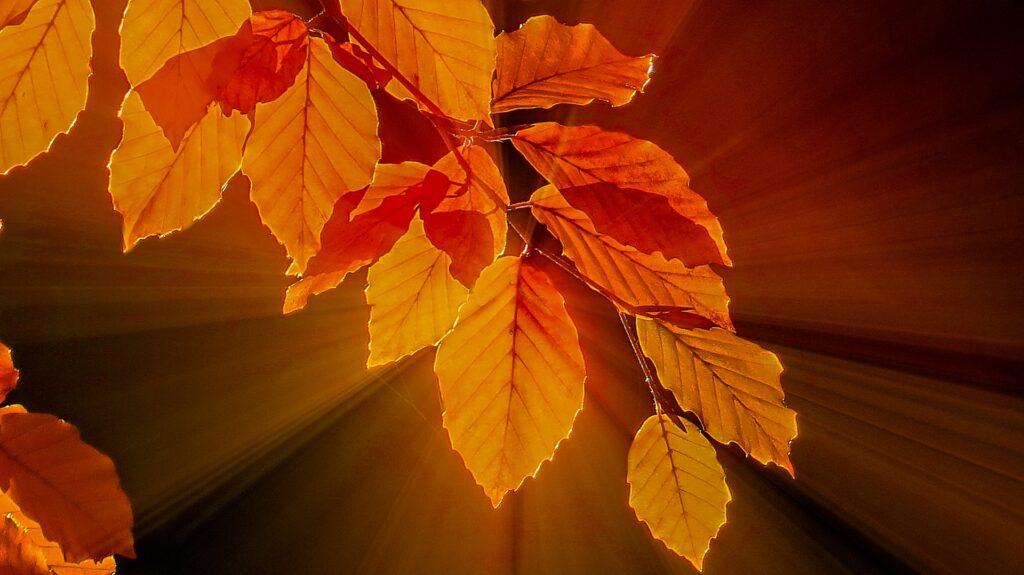
The pinkish-brown colour of beech with its fine tight grain and diffuse porous growth rings makes beech an attractive wood. It is easy to get a nice finish and it takes detail very well. I think beech is one of my favourites and is among the best wood for turning.
Challenges of turning beech bowls
Some people report that beech can warp or crack. Personally, I’ve not experienced that. It is harder than some woods, therefore you will need to sharpen your tools more often.
Silver Birch

The heartwood of silver birch can be a light reddish brown with nearly white sapwood. There is so little distinction between the diffuse porous growth rings that birch can be a little dull and uniform in appearance.
Challenges of turning birch bowls
Birch is fairly easy to turn and provides a good finish due to its close grain. The real challenge comes in storing birch for any length of time as it is vulnerable to insect attack and rots quickly when outdoors.
Walnut for Bowl Turning
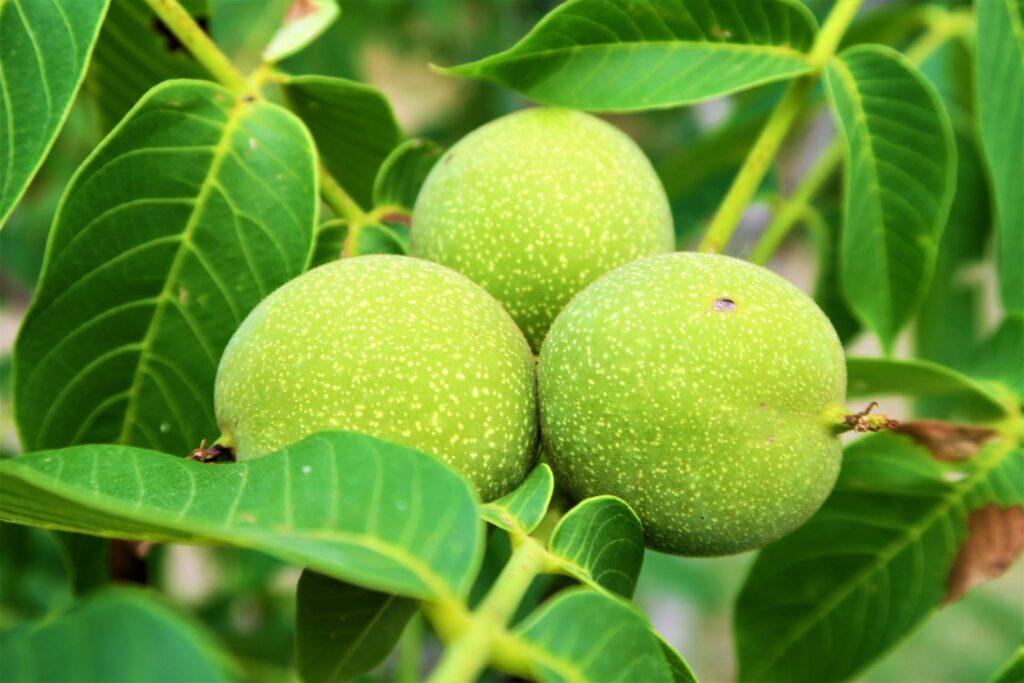
Fresh walnut is a lovely wood to turn and once oiled it is truly beautiful. Walnut has a tight grain that takes a finish well. Black walnut has a very dark heartwood and light sapwood that if integrated into a piece can make the item really stand out. Walnut (including Black Walnut) – is generally classified as semi-ring porous, which means it does not fit neatly into either category but has characteristics of both.
Challenges of turning walnut
Walnut dust can be an irritant. Therefore, I recommend that you wash your hands often and take a shower when you finish turning. You may also want to wear an appropriate dust mask. However, I would expect this to be more of a problem for power lather turners rather than a pole-lathe. With a pole-lathe you won’t generate anywhere as near as much dust as you will on a power lathe.
Sweet Chestnut for bowl turning
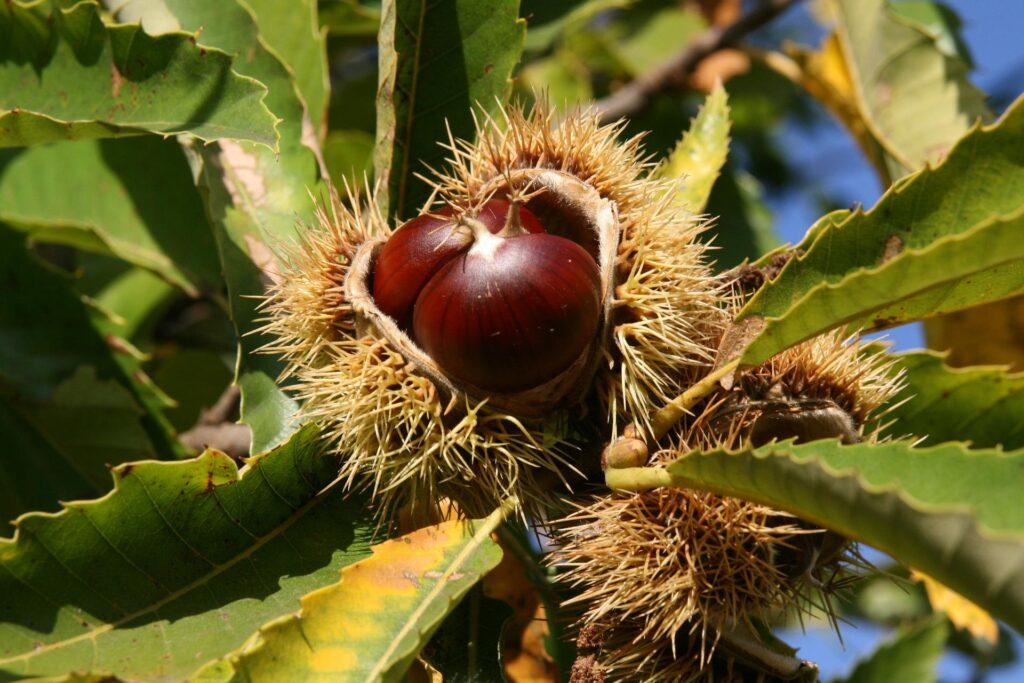
Sweet chestnut is a diffuse porous hardwood known for its durability. It is easy to split and is highly resistant to rot. It also turns very well and will make a very attractive bowl.
Challenges of turning Sweet chestnut
The wood will “move” or warp during the drying process. Electric lathe turners may choose to allow their bowl to dry and re-turn it. As a pole-lathe turner, I embrace the characteristics of the wood. As with most wooden bowls that warp as they dry, you end up with something unique.
Apple (Fruit Wood)
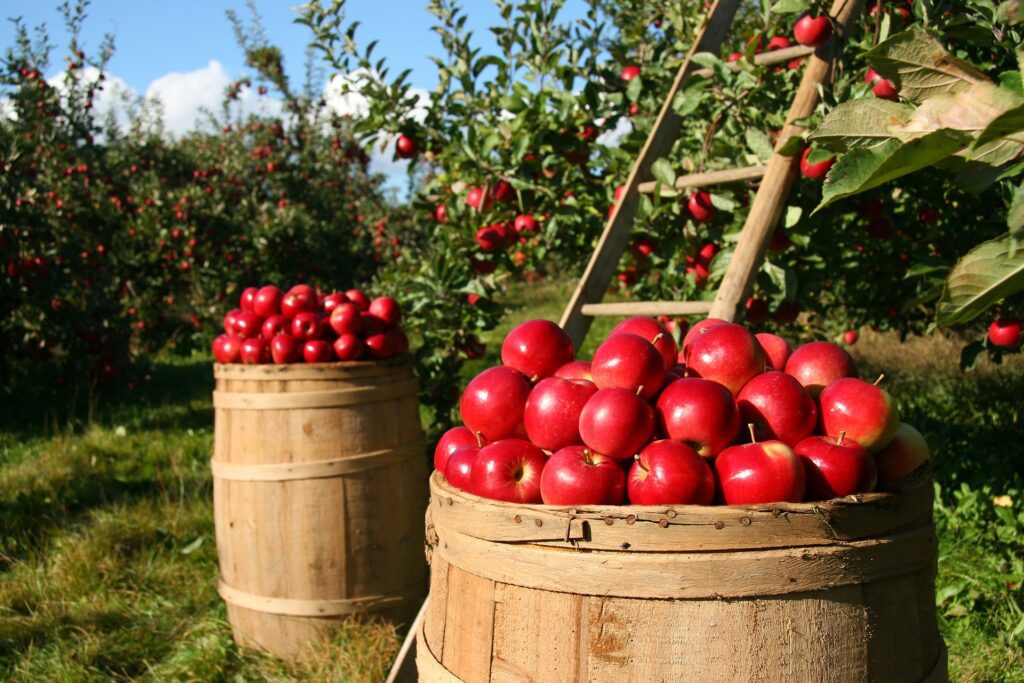
Apple and other fruit woods (plum) share similar characteristics. The grain of fruit woods can come in a range of colours and will provide a good finish. The diffuse porous growth rings provide a lot of character.
Challenges of turning fruit wood bowls
Like cherry, fruit woods tend to crack quite easily. Therefore a good drying routine is vital to reduce the number of bowls that fail due to cracks.
Ash for bowl turning

Ash is a very common wood at the moment. However, it is going to become less common because Ash dieback is becoming a larger problem in the UK. It is a strong durable wood that delivers a good finish. However, it does tend to split easily and in straight pieces. This makes it ideal for making furniture but can prove a little challenging when turning.
Challenges of turning Ash bowls
With all projects, it is best to use sharp tools. This is vital with Ash to achieve the best finish. You need to take care when working near the rim of the bowl. As mentioned Ash splits easily, therefore if you catch the rim where the grain is shortest it is easy to knock out a section of the bowl.
Glossary of Terms
1. Greenwood: Wood from trees that have recently been felled and have not yet dried out. It retains much of its natural moisture content, which can influence the woodturning process.
2. Checks: Cracks that develop in wood as it dries, typically occurring at the ends of logs where moisture escapes more rapidly than from the sides.
3. Earlywood and Latewood: The parts of a growth ring in a piece of wood. Earlywood forms at the start of the growing season, featuring larger, thinner-walled cells for rapid growth. Latewood forms later in the season, with smaller, thicker-walled cells that are denser.
4. Ring Porous Woods: Woods in which the earlywood has large pores and the latewood has significantly smaller pores, creating a visible ring pattern. Examples include oak and ash.
5. Diffuse Porous Woods: Woods where the pores are evenly distributed throughout the growth ring, without a noticeable transition from earlywood to latewood. Examples include maple and cherry.
6. PVA Glue: Polyvinyl acetate, a type of adhesive used in woodworking to seal wood pores and prevent excessive absorption or loss of moisture.
7. Sapwood and Heartwood: Sapwood is the outer, younger part of the wood, usually lighter in color and active in sap transport. Heartwood is the older, central part of the wood, typically darker and denser, providing structural support.
8. Woodworm: A common term for the larval stage of wood-boring beetles that feed on wood, often causing structural damage.
9. Tear-out: A defect that occurs during the woodturning process when chunks of wood are unintentionally removed, leaving a rough surface.
10. Wood Lathe: A machine tool that rotates a piece of wood about a horizontal axis against a tool that shapes it. Used in woodturning to create symmetrical objects like bowls.
11. Wood Pile: A stack or pile of cut wood stored for future use, often left to season until it reaches an optimal moisture level for specific woodworking projects.
12. Wood Turning: The craft of using a lathe to make wooden objects. It involves cutting, sanding, and shaping wood as it spins around a pivot point.
Thanks Jon, interesting article, well written and informative. I now know a little about a subject that I knew nothing about.
Thanks Dave,
I hope all is well with you and yours. Will I see you at one of my courses?
Jon